SERIES: SOLUTION MAKERS
Published December 16, 2021
Above Your Head
Western Pacific and Quality Material Handling optimize existing space for manufacturer
Contributed by: Western Pacific Storage Solutions
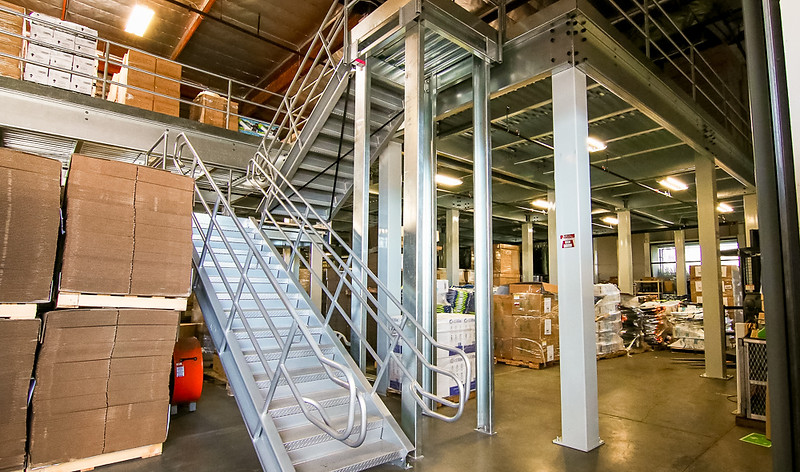
Sport Dimension had been pushing its facility to the limit when they contacted warehousing specialists Quality Material Handling. In partnership with Western Pacific Storage Solutions, Quality Material Handling embarked on an expansion project that would result in over 8,000 sq. ft. of additional storage capacity.
Over the course of a single year, Sport Dimension’s shipping demands had increased by 50 to 60%. This rapid growth created an urgent need for more space at their facility — a problem compounded by the company’s transition from primarily, a wholesale operation to a business model placing more emphasis on e-commerce.
Calculating their lease expiration date, Sport Dimension trawled the market for a building large enough to house their growing shipping obligations. After an abortive attempt to purchase a warehouse close to their existing facility, they turned to Ben Cisneros from Quality Material Handling known for their warehouse expertise. Because Cisneros recognized that a work platform, also known as a mezzanine, would play a primary role in the right solution, he brought Western Pacific on board.
The objective was to provide enough space for Sport Dimension’s storage needs in a way that was more cost efficient than breaking their lease and relocating to a new, bigger location. The answer lay not in the acquisition of a new site but within the existing space, above the very heads of employees.
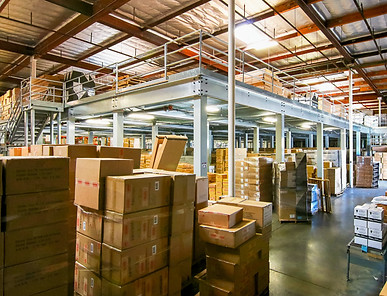

WPSS and Cisneros devised a plan that would maximize the space in four phases. The necessity of each phase would be reassessed upon completion of the preceding phase.
Phase One: A platform (mezzanine) above the shipping area, primarily for storing pallets.
​
Phase Two: Re-do the entire existing racking system to make it more efficient.
​
Phase Three: Add a second work platform (mezzanine) if necessary.
Phase Four: Knock through a wall to extend the space by 20,000 sq ft.
​
After securing the contract, the team had to overcome a series of challenges before work could commence on Phase One. Cisneros explained how they tackled the complex issue of mezzanine footing.
“Generally, on a platform of this size you would put in large concrete footings, but this was near-impossible in the timeframe we had to work with. So we engineered the work platform (mezzanine) in a different way, switching to 8 bolt column connections and increasing the supporting beams to around 20” per beam. This reduced the platform footprint size from 28”x28” to 16”x16” and shrunk the footplate from 2 ½’ x 2 ½’ footplate to about 1 ½’ - pretty nice for our customer.”
The team also found a way to cut the size of the work platform (mezzanine) in half.
“Initially, they were looking to do a much larger project with a 22,000 sq. ft. work platform (mezzanine),” Cisneros continued. “By offering the option of rearranging their entire racking system, we were able to reduce the size of the work platform (mezzanine) to 11,000 sq ft. Rather than looking for one cure-all solution to increase the space, we attacked the problem from multiple angles.”
​
This creative approach to construction resulted in the facility gaining 8000 sq. ft., over previously lost overhead space.
Furthermore, the construction team fitted the work platform (mezzanine) with sprinklers and a lighting system. The installation took less than five weeks, following a three-month wait for permits.
Throughout the project, WPSS remained close at hand.
“WPSS went to several meetings with the owners,” said Cisneros. “They made sure everything was done the correct way. We had multiple sets of eyes on everything.”
WPSS states that the key to their approach is “abandoning fixed ideas” about problem-solving.
“Finding a second warehouse is easy, obvious, and very costly. Lateral, outside-the-box thinking - which in this case required longitudinal, inside-the-box problem-solving was needed”.
​
At the time of this writing, Phase One has been completed and is awaiting final inspection. Customer satisfaction points to a high likelihood of work moving forward on Phases Two and Three in the near future.
​